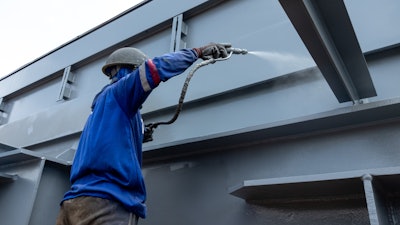
The two most popular fire-resistant coatings for warehouses are intumescent paint and cementitious coatings.
But if you ask ten warehouse managers which coating is better, and why, you’ll probably get ten different answers.
Each coating comes with unique advantages and disadvantages. Intumescent paints are extremely effective, but come with a higher price tag. Cementitious coatings are more affordable, but have their own drawbacks.
Let’s do a side-by-side comparison of the two coatings, looking at pros and cons of each, and talk about situations where one would be a clear favorite over the other.
Intumescent paint vs. cementitious coatings
You’re probably familiar with conventional heat-resistant paints. Well, intumescent paints have heat-resistant properties with added fire fighting protection.
Intumescent paints provide an extra degree of protection by expanding in the presence of high heat, protecting and insulating the substrate.
How does this work? Well, an intumescent coating is a chemical mixture suspended in a binder. When the coating is exposed to fire, the binder melts, and the suspended chemical mixture undergoes a rapid chemical reaction. Foam is produced, and the previously thin intumescent coating expands, becoming 25-50 times thicker.
That thickened fire-resistant foam provides tremendous protection to the substrate. If applied to steel, for example, it significantly lengthens the time before melting or collapsing.
Cementitious coatings are a little more conventional. For decades, concrete was a common fire-resistance measure because it was cheap — but it was also heavy and laborious to apply. Cementitious coatings are essentially a form of lighter concrete that’s mixed with paint.
But while they’re easier to apply than regular concrete, application is still quite labor-intensive, especially compared to something like intumescent paint. Cementitious coatings require a lot of surface prep before application, and then you have to apply several coats for maximum effectiveness.
They also come with some unique problems. When a cementitious coating dries, they tend to separate from the substrate. If moisture accumulates in that space, it will corrode the surface that the cementitious coating is there to protect. This is one reason why cementitious coatings are recommended for use in drier environments.
Pros and Cons
Let’s look at the pros and cons of cementitious coatings vs. intumescent paint.
When to use intumescent paint vs. cementitious coatings
The best fire-resistant coating for you is going to depend on factors like your budget, your substrate, and the function of your structure. Let’s touch on the ideal situation for each type of coating.
Cementitious coatings are much less expensive than intumescent paints, so if your budget is tight, this is the obvious choice.
Keep in mind, however, that they take several coats to be effective, so some of your savings on the coating itself will be eaten up by labor costs.
And cementitious coatings look like what they are — i.e. spray-on concrete. That’s a nice way of saying that they’re not nice to look at, so they’re best used on surfaces that aren’t public-facing.
Finally, the fact that cementitious coatings are prone to accumulating moisture between coating and substrate means they’re heavily recommended for dry environments. And their tendency to crack means they shouldn’t be used where they’ll be subject to impacts or vibrations.
Taking that all into account, the ideal application for cementitious coatings is somewhere that’s dry, non-public-facing, and easily accessible — for example, highway or roof structures.
Intumescent paints, on the other hand, are very aesthetically pleasing, and can look as good as a conventional paint or even a high-grade epoxy, with the proper topcoat. That makes them perfect for highly visible surfaces.
They also excel in moist environments, as they adhere very closely to substrates, locking moisture out.
Just keep in mind that local factors (like temperature, humidity, and dew point) at the time of application can have a huge effect on how well your intumescent coating adheres to the substrate. That means they’re best used in climate-controlled environments, where you can maximize their effectiveness.
They’re also great for mild or climate-controlled environments. However, local factors at the time of application like humidity, temperature, and dew point are a huge factor in how well (or how poorly) the coating adheres to the substrate.
So what’s the ideal application for an intumescent coating? Any surface that’s highly visible, in a moist environment, or climate-controlled. And if budget isn’t a consideration, their superior effectiveness makes them the better choice.
Just remember that facility managers need to consider NFPA and IBC guidelines, in addition to local guidelines, when choosing a structural fireproof coating.
Final verdict
Both cementitious and intumescent coatings offer great fire resistance, but intumescent paint is more versatile, more effective, quicker and easier to apply, and much more pleasant to look at (if also slightly more expensive).
Tommy O'Shaughnessy
Just keep in mind that facility managers should always follow IBC and NFPA standards when selecting fire protection. Top managers always consult with an expert coatings professional to get the best results and to make sure they’re in full compliance!
Tommy O’Shaughnessy is the owner of Industrial Paint and Protection Magazine, an outlet dedicated to helping facility managers, engineers, and contractors understand the world of industrial coatings.