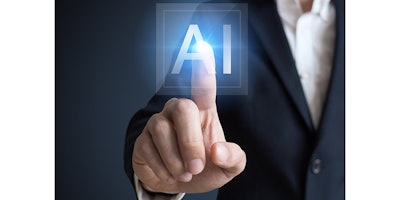
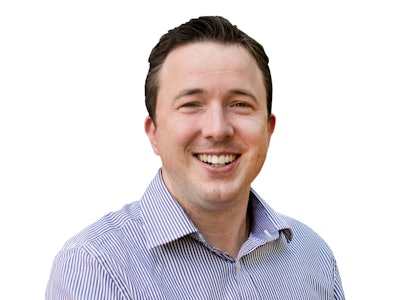
The history of predictive maintenance, or perhaps more specifically the crucial analysis of machine data that makes predictive maintenance possible, has long been dominated by laborious and expensive processes.
Typically, these would involve running a machine to failure, monitoring its components with sensors and recording the data produced during that period. The data would then be analyzed by experts for patterns of behavior and anomalies that would indicate wear, tear and signs of potential failure.
Even once this exhaustive preparatory work is completed, ongoing monitoring of machines and analysis of the data they produce still requires some level of manual intervention and interpretation from people with advanced analytical skills.
The levels of spending this approach required meant that early adoption of predictive maintenance was limited to pioneering sectors such as aerospace, where critical safety concerns clearly justified the cost of expensive data scientists and the development of new analytical techniques.
The results were spectacular. Instead of working to a predefined maintenance schedule or responding once a failure had occurred, aircraft engineers were able to provide the appropriate maintenance at precisely the right time. This reduced the amount of time wasted on unnecessary servicing and - more importantly - resulted in fewer components failing mid-flight and fewer aircraft falling from the sky.
The benefits of this approach have been recognized in other environments such as manufacturing and industrial plants where machine reliability is an important concern. The cost of employing data scientists and the level of manual intervention required, however, has meant that adoption has been largely limited to only the most critical and expensive assets.
Applying this kind of analysis across an entire plant or manufacturing environment would deliver significant improvements in machine uptime and maintenance efficiencies (by some accounts up to a 50% reduction in unplanned downtime), but it is simply too expensive to scale up this kind of labor-intensive approach across thousands of machines.
Upskilling existing engineering staff with data science skills has proven to be more trouble than it is worth. While both disciplines require a decent mathematical understanding, it can take years of intensive study to develop new data science skills from scratch. Engineers that do become competent data scientists tend to migrate to better paid, specialist data science roles in very little time at all.
Despite these limitations, the adoption of predictive maintenance by manufacturers and other large-scale industrial users has grown thanks to advances in artificial intelligence (A.I.). Many of the techniques used to transform aircraft maintenance and keep man safely in the air over the last couple of decades are being deployed at scale in more down to earth settings because the analysis of machine data can now be done automatically.
Any organization that is already gathering data from their machines for the purposes of incident logging or historical analysis can very quickly deploy automated predictive maintenance analysis across all of their monitored machines by connecting to advanced analytics tools, such as Senseye.
Automated algorithms chew through data from a range of outputs such as electrical current, vibration and torque levels. This enables the system to build up a detailed understanding of each components’ condition, and spot trends and unusual events that indicate when a particular part is getting closer to failing.
Using common data sets also helps to keep a lid on cost and allows the same analytical tools to be applied quickly to any machine from any manufacturer. Organisations can start assessing machine condition immediately using a series of algorithms that compare the machine data to known maintenance events. Crucially, the self-learning system teaches itself to become even more effective as it builds up a complete picture of each machine’s unique characteristics.
The ability to access this capability at scale is becoming increasingly popular. Nissan, for instance, is using Senseye's predictive maintenance capability to reduce downtime and increase overall equipment effectiveness across multiple global production sites where models such as the Qashqai, X-Trail, Leaf and Infiniti are produced. Over 2,500 assets, including robots, conveyors, drop lifters, pumps, motors and press/stamping machines are remotely monitored using Senseye’s algorithms, allowing technicians to optimize maintenance activities and make repairs months before predicted machine failure.
Elsewhere, in areas as diverse as pulp, paper and cement, heavy industrial uses are reducing the cost of downtime across all of their factory equipment by analyzing asset health data collected from different production and condition monitoring systems.
While traditional forms of predictive maintenance would have previously required organizations to recruit data scientists or retrain their engineers in a completely new set of skills, relying on A.I. to undertake monitoring and analysis of potentially thousands of machines requires only a shift in mindset and focus. The skills gap is filled by a virtual expert that has been trained across thousands of similar machines and is constantly improving itself.
Organizations already employing data scientists can leave the mundane day-to-day monitoring and analysis of machine condition to their A.I. assistant and focus their attention on the complex, systemic issues where they can add the most value.
Using A.I. to undertake the heavy lifting of condition monitoring delivers a substantial productivity boost to the maintenance department and beyond. Organisations that have already embraced this approach at scale have reduced their maintenance costs by 40 percent.
More than that, however, by monitoring all their machinery and not just the critical points of failure, manufacturers have also been able to reduce unplanned downtime by up to 50 percent and deliver dramatic improvements in throughput, quality and margin. The productivity gains associated with a virtual maintenance expert go way beyond the realms of maintenance itself.
Dr. Simon Kampa is the CEO and co-founder of Senseye.