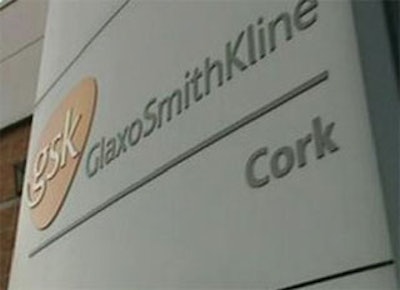
For too long, manual calibration methods have been accepted as necessary in pharmaceutical plants. No one questions the need to calibrate process instruments where accuracy and dependability are essential for quality and safety and to satisfy regulatory requirements. But we’ve been going about calibration in a traditional way that’s a lot of work and prone to error.
Management at GSK decided to investigate a number of generally accepted practices in 2009 and launched our Primary Supply Agile Engineering (PSEA) effort. Among other things, this team confirmed the high cost of existing instrument calibration procedures and issued a challenge to find a better way. As an automation engineer, I felt it would be necessary to implement technology in some way, but how? To find answers, we brought together a High Performance Team at our manufacturing facility in Cork, Ireland. Included in this group were knowledgeable representatives from the plant plus two suppliers — Emerson Process Management and Beamex Corp.
As a highly automated pharmaceutical plant, the Cork facility has more than 4,000 control loops, employing instruments from a range of manufacturers based predominantly on the HART® and FOUNDATION™ Fieldbus technologies. Our automation and instrumentation personnel knew all about the thousands of time-consuming calibration procedures done each year. Emerson is a supplier of measurement instruments and control valves, and their DeltaV™ automation systems control a good deal of production at Cork. Beamex is one of the world’s largest companies devoted to calibration solutions, and their MC5 portable calibrators and CMX software are widely used here.
The main objective of our High Performance Team was to find a better, faster way to calibrate instruments in order to reduce costs. It’s that simple. The Team soon began to focus on three areas where technology might be applied to achieve calibration excellence:
- Instrument diagnostics to reduce the number of calibrations on non-critical, non-safety-related instruments based on data generated by those devices.
- Paperless calibration by automating calibration procedures to shorten the time required and eliminate manual support functions.
- Calibration analysis to identify instruments for less frequent calibration while still meeting strict corporate and regulatory requirements.
Each of these areas is heavily dependent on the use of technology to achieve calibration efficiencies. In essence, we challenged our two technology suppliers, telling them what we wanted and trusting them with broad access to our plant and personnel in order to produce a solution.
Instrument diagnostics
Plant technical personnel were routinely calibrating instruments that they knew did not need the same level of attention as devices that were critical to product quality or safety. One of our first tasks was to determine which instruments could be moved from the periodic schedule to “on-demand” calibration, i.e. those instruments that are not directly involved in the production of our pharmaceutical products. This selection process was aided by examining the diagnostics generated by every smart field device and digital valve positioner.
Emerson’s AMS Suite predictive maintenance software is able to obtain data from field instrumentation, either by monitoring for changes in their condition or by contacting them one-by-one from a central location. Although the information was available previously, we were not utilizing it to tell us when an instrument needed calibration. So we began monitoring a select group of less critical instruments, waiting for them to indicate that a change has taken place internally requiring attention.
This condition monitoring program is the basis for on-demand calibration, which has eliminated 234 calibrations per year so far. The calibrations that are now done on-demand are also performed in a more efficient manner.
Paperless calibration
Streamlining the regular calibration procedure is based on optimizing periodic calibration schedules, using documenting calibrators, and synchronizing instrument data between Beamex’s CMX calibration management system and Emerson’s SMA Suite. Paper is totally eliminated in the process, and substantial savings are accrued.
Calibration data on every instrument is stored in the AMS Suite database and downloaded at the appropriate time directly to a MC5 portable calibrator for use by a technician following a designated route in the field. When the scheduled calibrations are completed, the results are uploaded to the CMX analytical software for certification and then returned to the instrumentation database for documentation.
This new procedure cuts about 15 minutes from each calibration, saving hundreds of hours on the thousands of procedures done annually compared with the time required for the paper-based method. In addition, it is no longer necessary for administrative personnel to spend up to 10 hours per week manually entering data recorded by technicians on sheets of paper.
However, this system required an innovative method of linking two distinctly different software packages. The AMS Suite serves as the source of current data on each instrument which is used by the calibrators in the field. Beamex’s CMX software is tightly integrated with AMS Suite to manage the calibration program, including advanced scheduling and data analysis. Its comprehensive certification and reporting package provides everything needed to comply with 21 CFR 11, our main regulatory requirement. Achieving connectivity between these two software packages was the key to automating our calibration.
Calibration analysis
A final piece of the puzzle involved extending the interval between calibrations, where possible, in order to reduce the overall number of procedures done annually while remaining in compliance with corporate policy and the regulations. This is being achieved through an on-going, computer-driven analysis of historical data to identify instruments that do not need to be calibrated as often as some of the others. This group includes quality and safety related instruments calibrated on a schedule, but we want to do those calibrations on the RIGHT schedule.
Many instruments in our plant are now calibrated yearly rather than every six months, and their condition is closely monitored to be sure they continue to perform as designed with no compromise on quality.
Pilot project
Beginning in November, 2010, a number of critical instruments that showed no tendency to underperform were switched to annual calibration, and other non-critical devices were selected for on-demand calibration. These numbers are increasing as we go along, but we estimate it will take three to five years before our goals are fully attained.
Our new, automated calibration procedure is firmly in place as we continue to carefully watch the condition of all production-related instruments to be certain they are not under-calibrated. But, of course, we don’t want to over-calibrate, either. That’s what this program is all about, because a lot of savings can be realized through on-time calibration.
Results
The judicious application of technology has enabled this facility to achieve savings in a number of ways:
- Time per calibration reduced by at least 15 minutes, equating to hundreds of hours saved doing thousands of calibrations
- 21,000 sheets of paper eliminated each year
- More than 500 hours per week of manual data entry time eliminated along with potential errors
- 8 percent reduction in scheduled calibration attained through data migration from legacy system
- 234 calibrations eliminated yearly by extension of calibration intervals
- 33 percent of instruments not directly related to quality or safety removed from scheduled calibration and done on-demand, producing an annual saving of approximately 300 hours.
We have a good idea here, and every saving is perpetuated because it is not a one-time thing; hours saved one year continue year-after-year. In addition, automated calibration is applicable wherever instruments operate in process industry plants. In fact, the company is considering extending this program to other GSK facilities worldwide.
For more information, please visit www.emersonprocess.com.