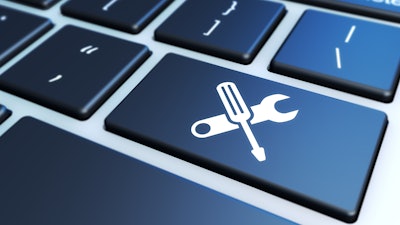
‘Machine not working’ - that is fundamentally what downtime in the manufacturing world is about.
And any manufacturer knows that machines not working under normal circumstances means loss of productivity and losses in revenue. Unplanned or poorly-planned downtime can disrupt production schedules and result in delays that impact orders and production targets. No manufacturing company wants that - nor can they afford it.
The cost of downtime can be incredibly high for any manufacturer, especially since downtime is the Number 1 reason for loss of production, resulting in factories losing up to 20% in total productivity. Downtime results in a series of costs and losses, both tangible and intangible, including production, labor, replacement costs, product losses and reputation damage.
Unplanned downtime is the real killer. A 2018 report titled After The Fall: Cost, Causes and Consequences of Unplanned Downtime surveyed 450 professionals from 350 companies in the UK, U.S., France, and Germany across various industries, including manufacturing, and found that the cost of unplanned downtime was approximately $250,000 per hour, at an average of more than $2 million per downtime event.
The survey also found that 82 percent of companies had experienced an unplanned downtime event in the previous three years, while 70 percent admitted they did not have complete awareness of when all their machinery was due for maintenance or upgrade. Of course, different companies will have different rates of downtime.
Beyond Proactive
When it comes to maximizing downtime, maintenance is hugely important. Or, rather, intelligent maintenance is what makes the difference.
Some people may still assume that maintenance is a proactive measure at best. But with the advent of smart technology in the maintenance realm, predictive maintenance is what any manufacturing company should be implementing today. Deloitte views predictive maintenance as the pinnacle of maintenance regimes, at Level IV, compared to reactive maintenance (Level I), planned maintenance (Level II), and proactive maintenance (Level III). It can also result in an overall equipment effectiveness (OEE) rate of 90 percent or more.
A viable way to aim for predictive maintenance is with the help of a computerized maintenance management system (CMMS). Accurate prediction creates greater certainty and, hence, better maintenance results.
There are many reasons why a manufacturer should upgrade or switch to a CMMS, including the most obvious one: Being able to know ahead of time when repairs to machinery or equipment may be due. Another reason is that a CMMS allows you to ‘stay in the loop,’ whereby you can be on the move and not have to be desk-bound in order to be up on maintenance developments.
Keeping It Simple
Predictive maintenance doesn’t need to be hellishly expensive or complex. For small or medium-sized companies, even simple, fairly inexpensive measures can be implemented in the transition to predictive maintenance. These can include the installation of low-cost sensors, which detect mechanical or environmental factors, such as heat, vibration, and temperature that can cause equipment or machinery damage or failure. This data can then be transmitted to a central point so that production management are alerted about issues arising. This in turn greatly assists in reducing the need for costly, time-consuming downtime.
Total productive maintenance (TPM) is the interaction between machinery, equipment, and the workers who use them, as well as the systems needed to maintain both proactive and predictive maintenance measures. Employee training on machinery and, where possible, their active participation in the maintenance thereof, is considered key. TPM can also greatly improve a company’s OEE over time. It can be considered the ‘culmination’ of predictive maintenance. Therefore, it could be said that TPM strives for ‘perfect production,’ with no defects, breakdowns, stoppages or accidents.
Invest in Your People
The number one cause of downtime is not due to machinery or equipment breakdowns - it’s humans. Or, rather, it’s human error, particularly in manufacturing. In fact, a 2017 survey found that human error causing unplanned downtime is more common in manufacturing than in any other sector. This shouldn’t be surprising given how heavily reliant the industry often is on heavy machinery that is complex and expensive. Industrial hygiene factors such as noise, heat, and ergonomics can further exacerbate the complexity of working with machinery, with resultant worker errors.
Maintenance, therefore, cannot only be about predictive software and proactive procedures. It also needs to be about the people who operate, manage, or otherwise interact with machinery and equipment. Even the growing automation of manufacturing plants in the U.S., for example, “has caused a simultaneous need for maintenance workers who can maintain, troubleshoot, repair, and operate the equipment.”
Maintenance is here to stay. The following checklist should help put people at the very center of your maintenance program - where they belong:
- Train, train, train = investing in risk-aware, proactive workers.
- Encourage dialogue = quicker reporting of potential maintenance-related issues.
- Cross-functional teams = more depth and diversity of know-how means issues can be diverted in good time.
- Contextualize maintenance within a risk-savvy culture at all times = encouraging cooperation and belief in the company’s maintenance program.
If manufacturing is essentially about ‘making things,’ then every effort must be made to maximize those times when things are not being made due to downtime. Every company has to make concessions regarding downtime. However, it is the way in which concessions are made which makes all the difference. Maximizing downtime is not only intelligent - for a company’s bottom line, it’s intelligent manufacturing.