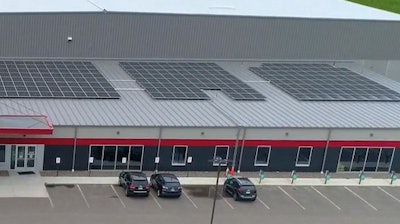
Production at Trystar was temporarily halted in 2018 when a tornado ripped through the outskirts of Faribault, Minnesota, causing extensive damage and widespread power outages.
Though Trystar, an electrical equipment designer and manufacturer, frequently responds with alacrity to disasters by building and delivering electrical equipment to its affected customers, the tornado was the first time a monumental weather event affected it at home.
An aging and overstressed grid, its recollection of the Faribault tornado and a keen interest in reducing carbon emissions led Trystar to design and build its own microgrid to help ensure continuous productivity.
Guarding Against Outages
An emergency power system consisting of generators, transfer switches, controllers and onboard or stationary load banks is a common approach to ensuring continuous power. However, Powering Trystar’s entire facility and full production capacity would require a significant capital investment.
Therefore, the company decided to develop a more focused and largely sustainable standby solution, producing enough power to ensure worker safety, limited production and lighting. Trystar was also interested in peak shaving benefits. Given Trystar's considerable experience designing, engineering and building docking stations, it would incorporate a docking station as part of the microgrid system to accommodate an extended outage.
Docking stationTrystar
Trystar initiated the project by metering loads across the enterprise and studying peak usage by equipment and time of day over a year. It also analyzed the startup rates of machinery versus operating rates and how they impacted utility usage.
The company then collaborated with a system integrator and power utility provider to review its needs and ensure alignment with microgrid system best practices and critical design considerations. This approach helped Trystar select combinations of energy sources to support its sustainability and resiliency goals: solar, wind and a battery energy storage system (BESS).
The first step was to install 320 solar panels on the factory roof. The solar panels offer 172.8kW of combined potential output. The panels are connected to a central inverter, which converts the solar panels' direct current (DC) into alternating current (AC) that the factory can use. Simultaneously, contractors installed a 232kWh BESS.
InvertersTrystar
This system consists of a series of lithium batteries that can store excess energy produced by the solar panels and two 3.5kW wind turbines. When energy demand exceeds supply, the batteries can be discharged to provide additional power to the factory.
Understanding that conditions and power outage durations could drain reserves, Trystar also installed a 350kW (480 volt) natural gas standby generator to supplement charging and address peak demands as necessary. It operates cleaner than a diesel generator, and there’s no diesel fuel tank with which to contend. Trystar sized the system to power primary production needs, e.g., air hoses, power tools and lights.
As part of the microgrid and Trystar’s control scheme, its gas generator is cycled regularly. The natural gas design precludes the compulsory exercise associated with a diesel generator to avoid wet stacking.
The system constantly monitors energy production and consumption and adjusts energy flow accordingly. For example, if energy demand is low, the excess energy produced by the solar panels and wind turbines will be stored in the batteries for later use. On the other hand, if energy demand is high, the smart system will prioritize energy delivery to the areas of the factory that require the most energy. In addition to providing relief from an outage, the system is used daily for peak shaving.
Trystar played a very active role in the design and engineering of its microgrid. It designed a breaker pair with a controller between them to achieve automatic transfer switch (ATS) capability but at a large ampacity (3000A) using breaker pairing controller technology.
This ATS is located at the utility connection point to switch between utility and generator power. The main utility disconnect is located inside the unit. The unit also includes the temporary generator connection (like an ATS docking station Trystar produces as part of its product line).
Should the power outage last longer than anticipated, a portable generator can be brought in to handle the entire building load, allowing production lines to run at full capacity. Although not an instantaneous solution, the temporary connections facilitate hooking up a rental generator without requiring an electrician, and it's a quick process.
TurbineTrystar
Leveraging the Experience
"The new microgrid is one of the first steps in our journey to protect our natural resources and ensure the future of generations to come," Aaron Padrnos, Sr. Manager of Customer Experience and project lead, said. "It also keeps us operational should production be jeopardized by a weather event or grid failure. Yet, the microgrid also serves as a practical laboratory. For example, it led to the development of our 3000-amp transfer switch. We also developed a PLC and software (i.e., a master controller) in-house to coordinate and control all the unique power sources (solar, BESS, wind, utility and generator) in the system. The program constantly monitors the facility’s power usage and leverages the separate power sources with a control scheme to help Trystar peak shave. It's also programmed to respond to a complete outage.”
The microgrid allows Trystar to gain better insight into the renewable space, including solar power, battery storage and the interconnectivity between microgrids and utilities. It recently developed the capacity and signed the agreements to sell excess energy back to the utility.
The microgrid project also inspired Trystar to extend its new acumen to its customers. It recently designed and built a portable microgrid called the Trystar GridPak. The GridPak is comprised of solar panels and a sophisticated BESS, supplemented by a natural gas generator. It's a cleaner alternative to a conventional diesel or gas portable commercial generator.
Trystar
“The microgrid will support our sustainability journey and those of our customers by allowing us to create and validate new energy solutions and systems," Padrnos said. "From a practical standpoint, it helps us economically through peak shaving and by helping us ensure production in the event of an outage. Even if you're in an area where you don't expect a power outage due to a natural disaster or grid failure, other things could limit power to your facility. Things happen. Our answer was leveraging Trystar's know-how to build a unique microgrid solution to meet our needs."